Results
Solution
The business challenge
Running Operations more Predictively
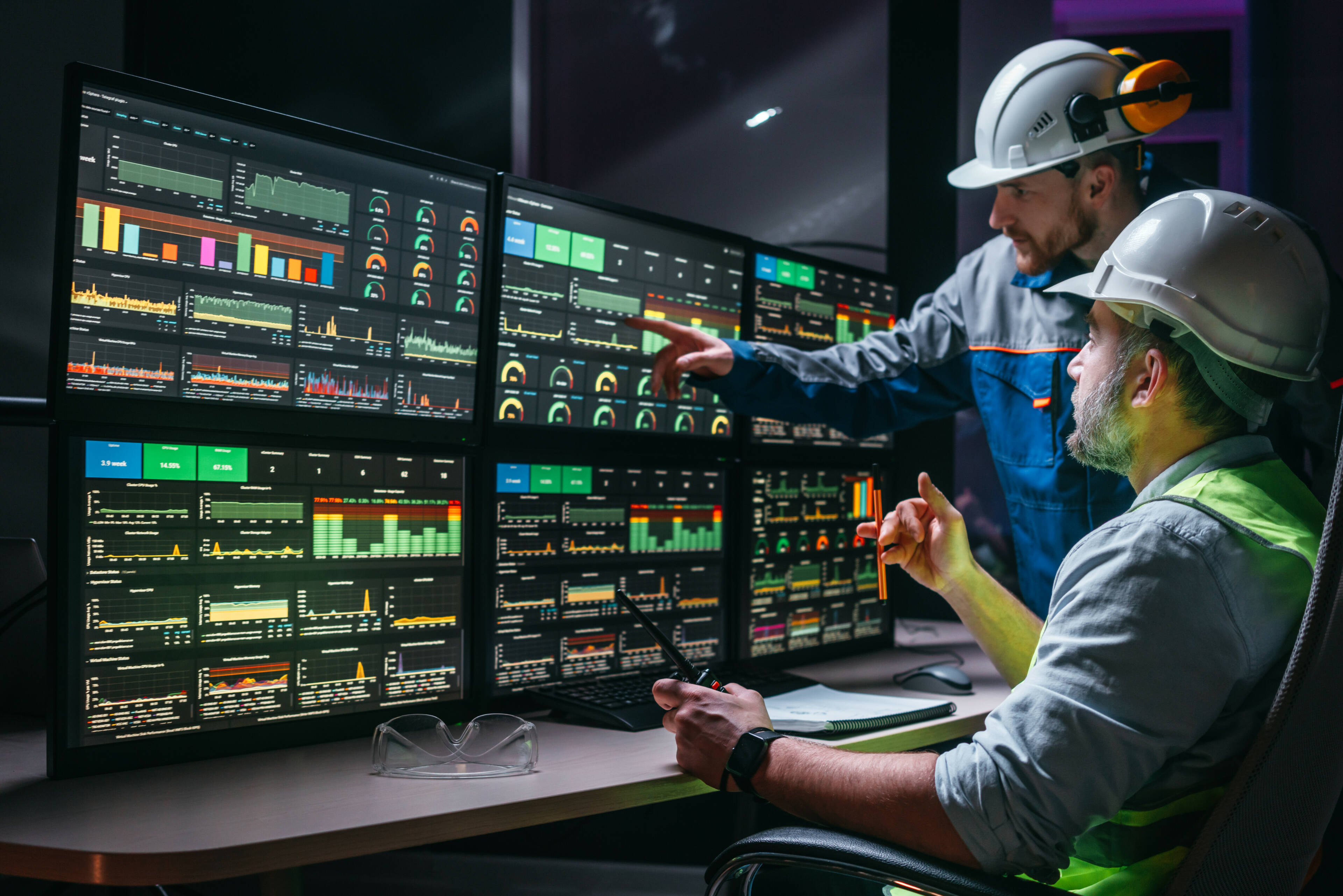
The business challenge
Our client is a major supplier to some of the biggest agricultural product producers in the world. The company creates chemical products for the manufacture of fertilizers, herbicides, and pesticides, and operates several large processing units in the Nordic region. These processes are dependent on the use of heat, so the requirement for energy is high, particularly because of the cold climate.
The company recognized that it was not operating in the most optimized manner. Orders arrived in an uneven pattern, which made planning very difficult. Raw material stocks and resources were not closely aligned with demand and production units were not always fully occupied, yet they continued to operate all units, deploy critical resources and consume energy throughout the year.
To improve efficiency, and ensure the longevity of the business, a more holistic view of the entire operation was required.
The solution
The manufacturer called on us for help. We began by conducting a deep-dive analysis across the entire operation. Utilization levels, headcount, and cost per unit were all taken into account. We also looked at the company’s order book to understand the “demand signals” being received from customers.
The next step was to construct a central “control tower/command center” which would provide the management team with an overview of the essential information required to run the business day to day, in some cases utilizing short interval control.
This included key information from each unit such as raw materials usage, labor deployment and productivity, energy consumption, and demand patterns. To allow for rapid decision making, this information had to be understood quickly so visualization was crucial. A dashboard driven KPI approach was put in place for the operations leadership team that cascaded down to individual units, so there was an aligned approach to the adjustments that would maximize performance.
An operations model with analytics was also constructed to run scenarios that showed how units could be optimized, covering everything from operating costs to the flow of demand from customers, and the incoming supply of materials. From this, an operating plan was developed for the coming months.
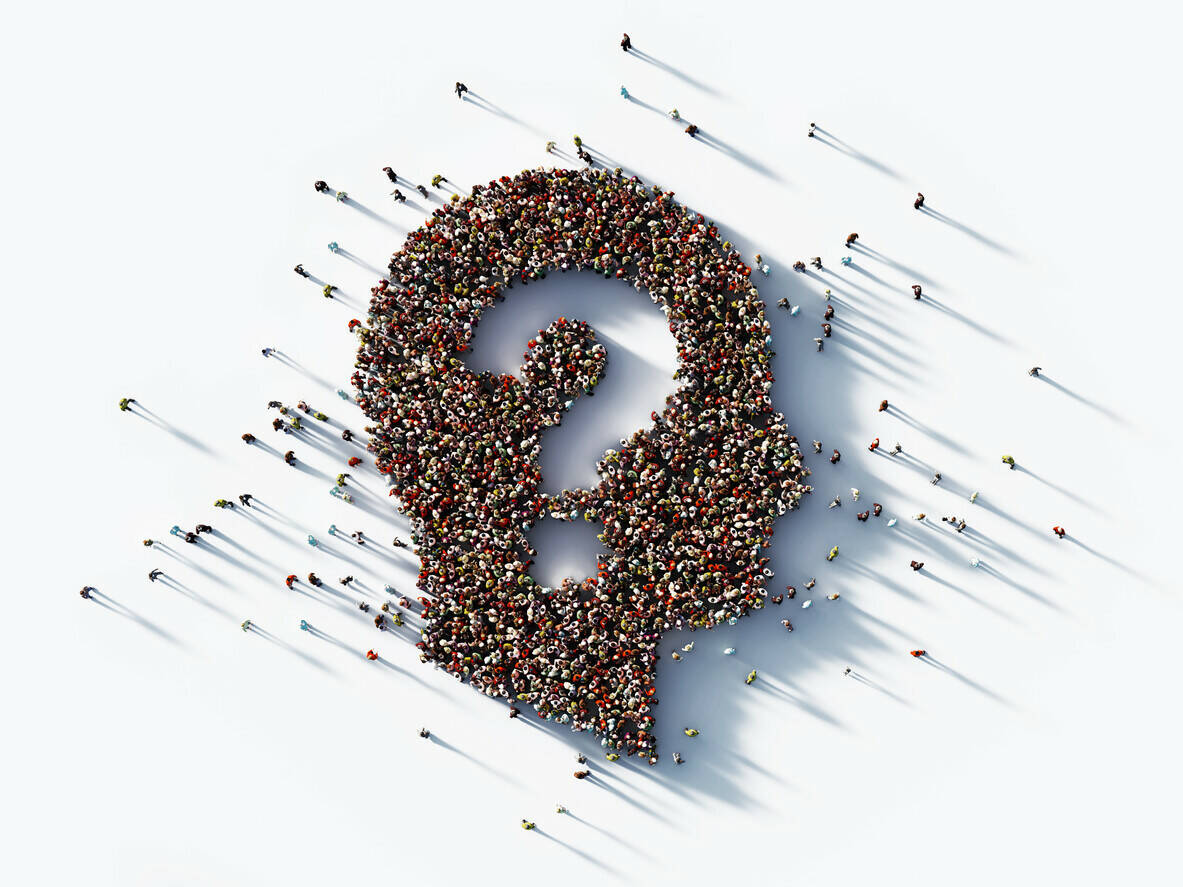
Results
With the insight obtained from the control tower/command center, the company concluded that considerable cost savings could be made by temporarily closing units if they fell below a particular level of KPI. With the centralized dashboard in place, these KPIs can be easily assessed, and decisions taken very quickly.
The efficiency gains from this new model meant that the company was able to match its output to demand while optimizing the capacity of its processing units. By idling units when demand fell below set levels, the company was able to significantly improve EDITDA.
The company’s sales and operations planning (S&OP) was also improved dramatically. The visualization of different parts of the supply chain made it possible to precisely manage and plan production, material, energy, and logistics – and customer satisfaction was also improved.
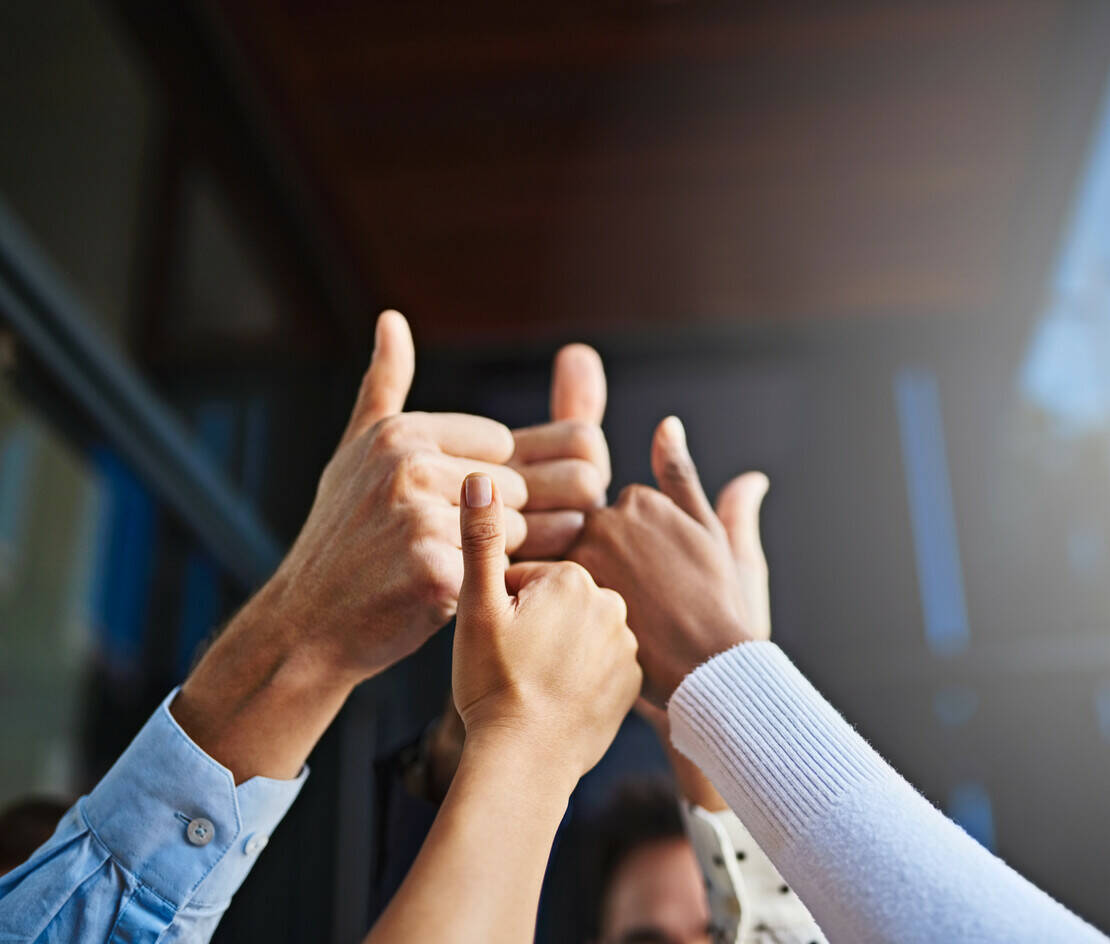
6 months
Project duration
Nordic region
Location
Agri chemicals
Industry
With the insight obtained from the control tower/command center, the company concluded that considerable cost savings could be made by temporarily closing units if they fell below a particular level of KPI. With the centralized dashboard in place, these KPIs can be easily assessed, and decisions taken very quickly.
The efficiency gains from this new model meant that the company was able to match its output to demand while optimizing the capacity of its processing units. By idling units when demand fell below set levels, the company was able to significantly improve EDITDA.
The company’s sales and operations planning (S&OP) was also improved dramatically. The visualization of different parts of the supply chain made it possible to precisely manage and plan production, material, energy, and logistics – and customer satisfaction was also improved.
Results
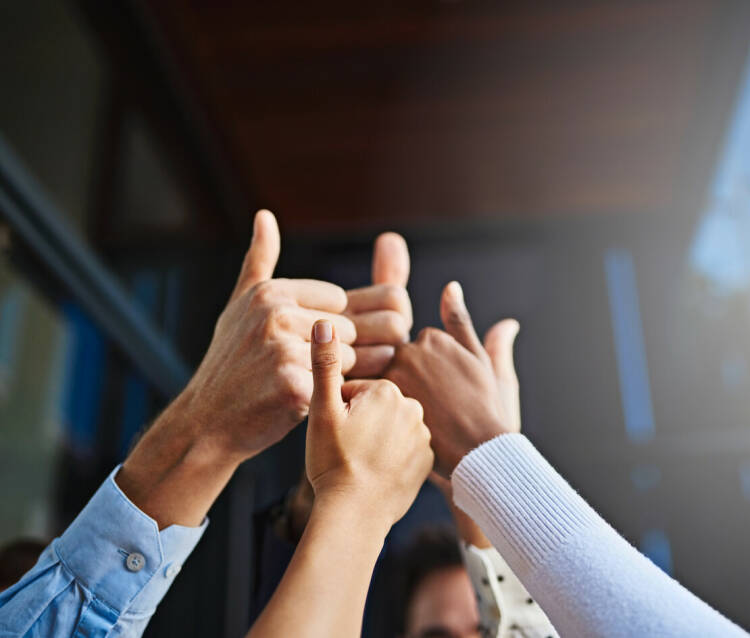
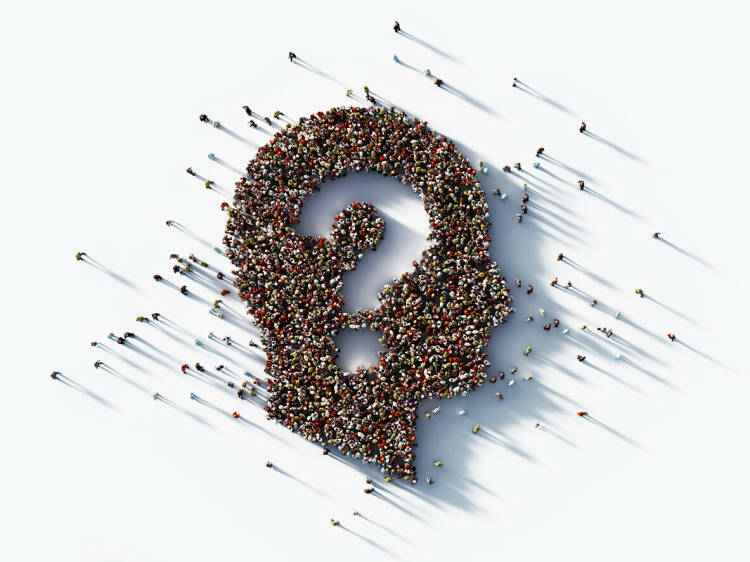
The manufacturer called on us for help. We began by conducting a deep-dive analysis across the entire operation. Utilization levels, headcount, and cost per unit were all taken into account. We also looked at the company’s order book to understand the “demand signals” being received from customers.
The next step was to construct a central “control tower/command center” which would provide the management team with an overview of the essential information required to run the business day to day, in some cases utilizing short interval control.
This included key information from each unit such as raw materials usage, labor deployment and productivity, energy consumption, and demand patterns. To allow for rapid decision making, this information had to be understood quickly so visualization was crucial. A dashboard driven KPI approach was put in place for the operations leadership team that cascaded down to individual units, so there was an aligned approach to the adjustments that would maximize performance.
An operations model with analytics was also constructed to run scenarios that showed how units could be optimized, covering everything from operating costs to the flow of demand from customers, and the incoming supply of materials. From this, an operating plan was developed for the coming months.
The solution
The business challenge
6 months
Project duration
Nordic region
Location
Agri chemicals
Industry
Our client is a major supplier to some of the biggest agricultural product producers in the world. The company creates chemical products for the manufacture of fertilizers, herbicides, and pesticides, and operates several large processing units in the Nordic region. These processes are dependent on the use of heat, so the requirement for energy is high, particularly because of the cold climate.
The company recognized that it was not operating in the most optimized manner. Orders arrived in an uneven pattern, which made planning very difficult. Raw material stocks and resources were not closely aligned with demand and production units were not always fully occupied, yet they continued to operate all units, deploy critical resources and consume energy throughout the year.
To improve efficiency, and ensure the longevity of the business, a more holistic view of the entire operation was required.
Running Operations more Predictively
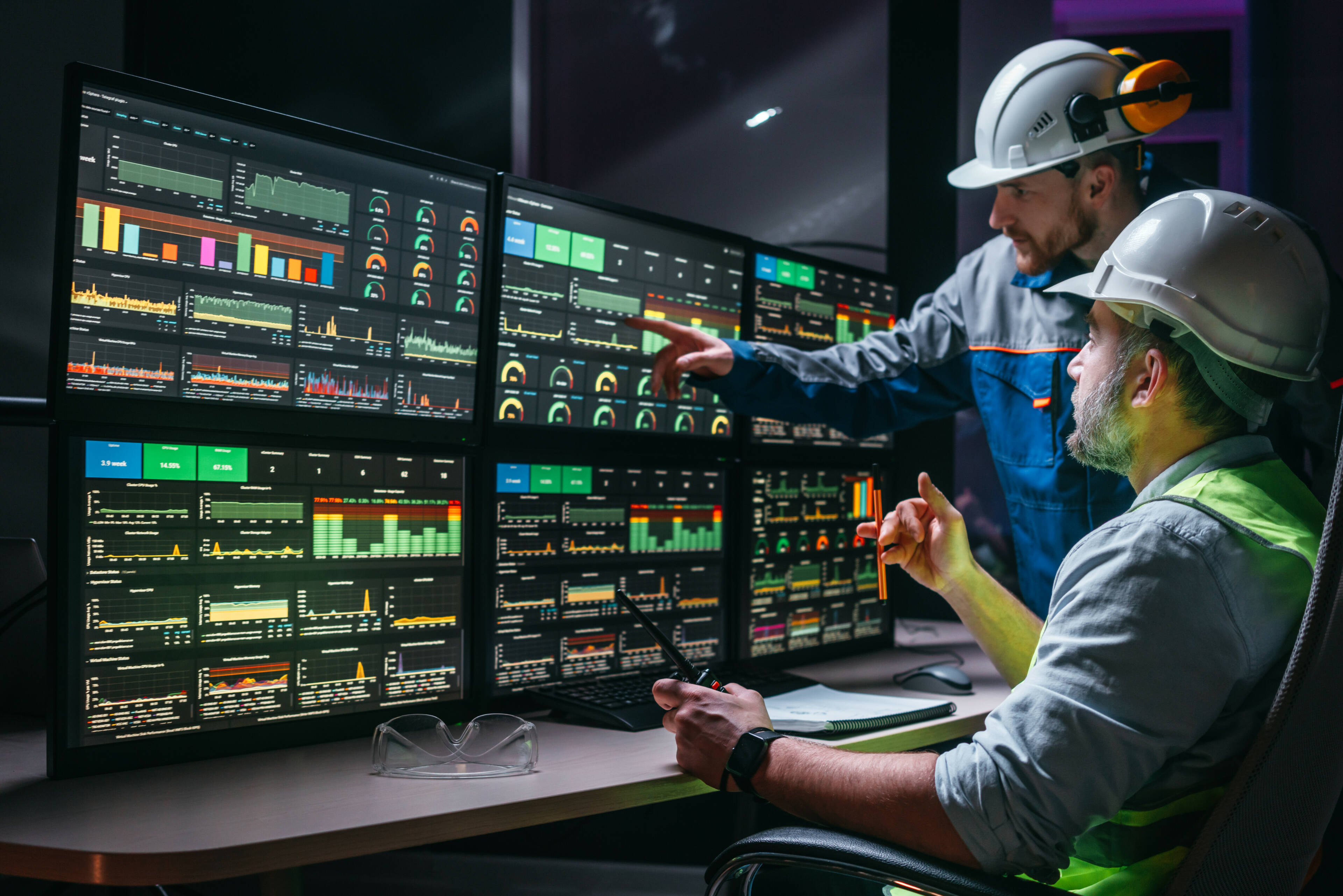