Results
Solution
The business challenge
Managing supply chain risk in a rapidly changing chemical industry
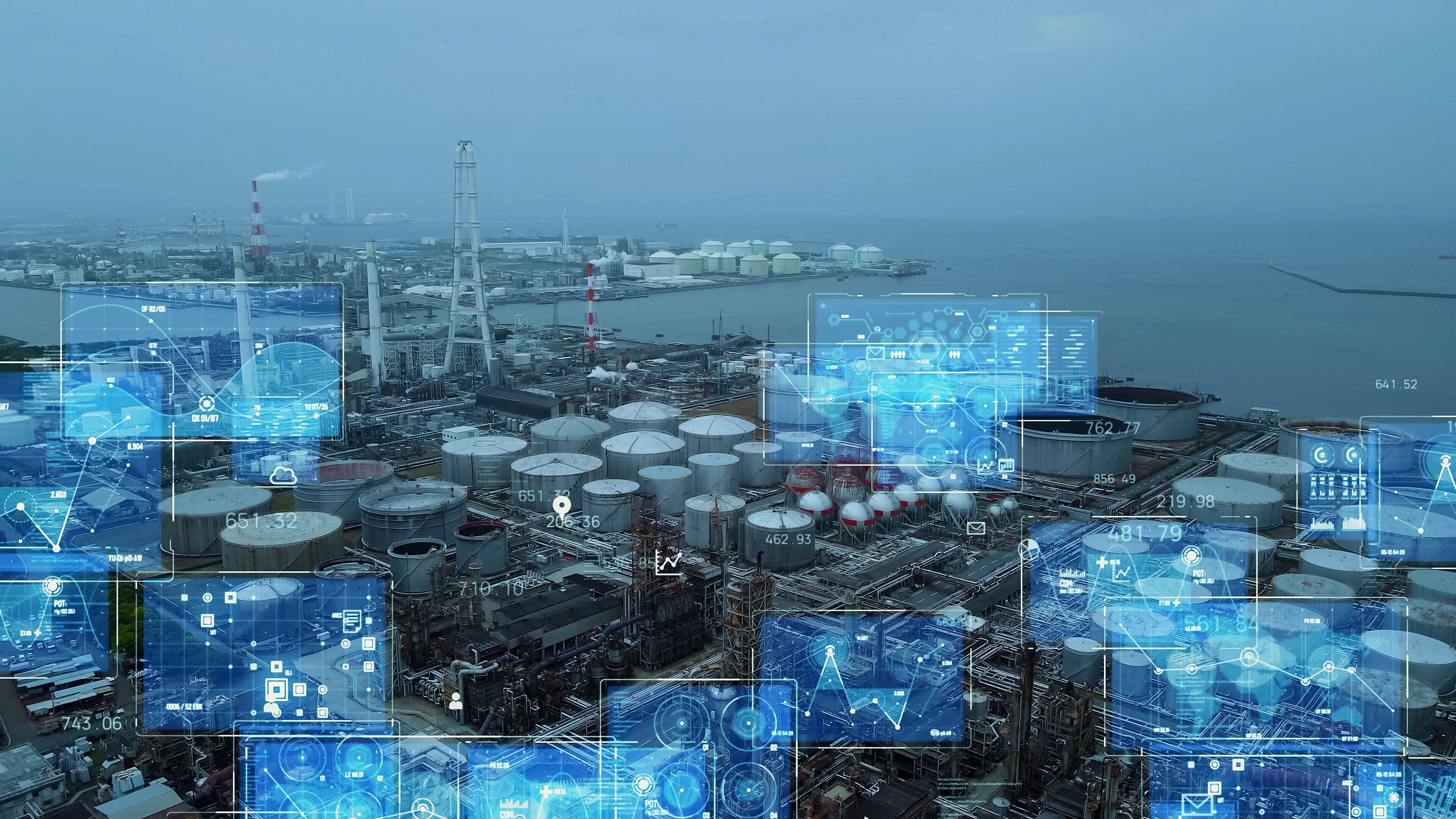
The business challenge
A European multinational chemical company could see that its product line was going to be significantly affected by several changes taking place in the industry.
New regulations in Europe meant key chemical components would no longer be permitted and this was going to have a huge impact on the market. The removal of these raw materials would mean certain products would need to be discontinued, while others would require alternative components to be introduced. These changes were going to affect the organization’s output capacity – and were already affecting its gross margins.
Alongside this, major developments in automation were quickly transforming the industry. Forecasts by the organization showed that if innovation continued at the same pace, demand for specific products from the buying industries would dramatically diminish.
While the business had access to the data needed to monitor key performance metrics across its value chain, it was struggling to interpret the information and understand how it could help to mitigate the risks it faced.
The solution
We were able to bring together extensive amounts of information and analyze how each of these risks would impact the business in terms of costs and performance over the long-term.
We demonstrated where the business would likely be in 10 years’ time if no action was taken. We then shared a ‘worst case’ scenario which showed output would decline to just 15% of current volumes. We also highlighted the impact this would have on costs and how it could potentially lead to facilities closing – and how that might lead to the loss of staff and damage the company’s reputation.
We then simulated scenarios that could mitigate the risks. This included exploring substituting raw materials and outsourcing or insourcing certain elements of its operation to save costs. We also developed a reaction plan defined by a series of risk events and mapped out how the business should respond to each risk if they ever came to fruition.
Finally, we created a ‘digital twin’ of the organization which would track operational and financial data. This would enable the business to set an alert level for each risk event.
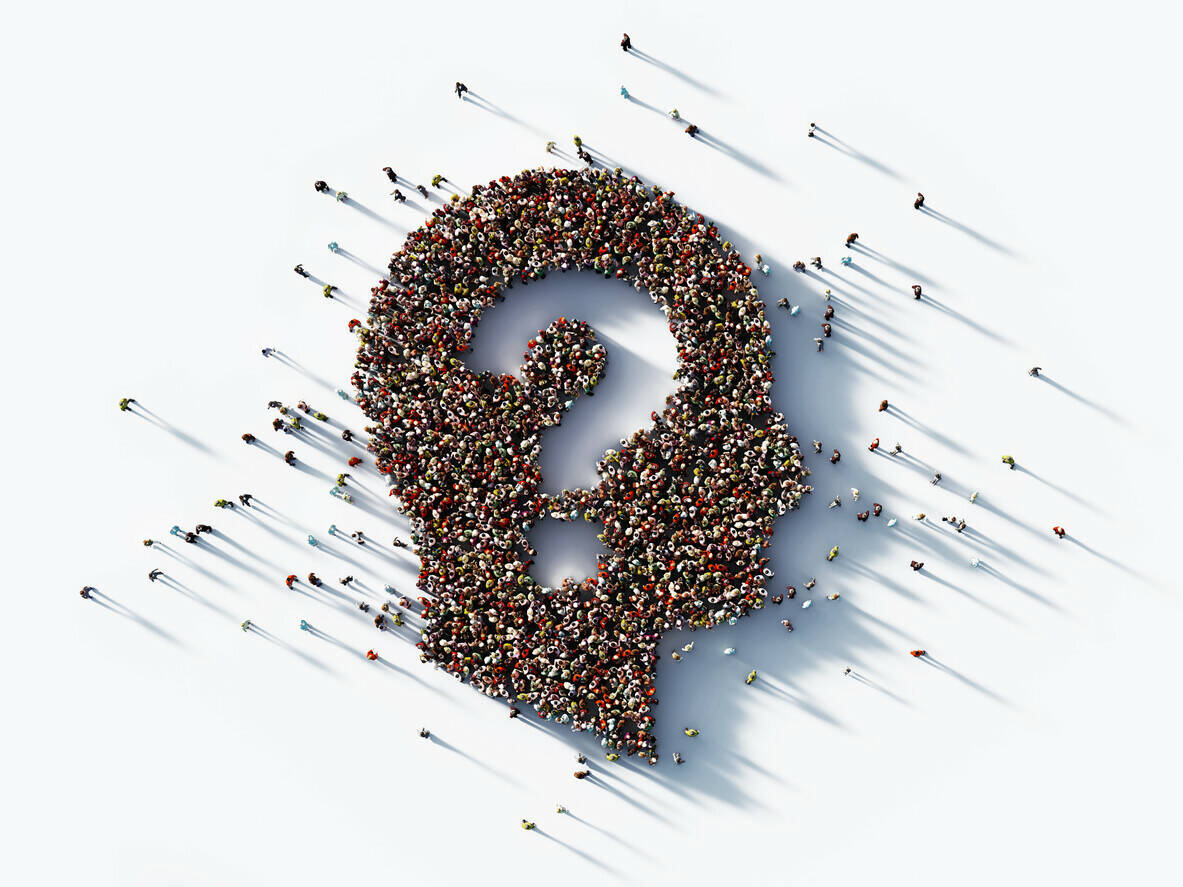
Results
The ability to monitor risk and react to different scenarios has helped the business achieve an uplift in gross margins of 8%-10%. The organization is now also prepared to mitigate changing legislation, as and when this happens, with recovery options in place and ready to go.
These steps have helped the organization understand not just what actions need to be taken, but when would be the best time to react and mitigate changes in the industry. By considering all the relevant factors, and bringing together all the necessary data, the company can now quickly make complex decisions that will determine the ongoing viability of its plants – ensuring on the ongoing success of the business over the next 10 years.
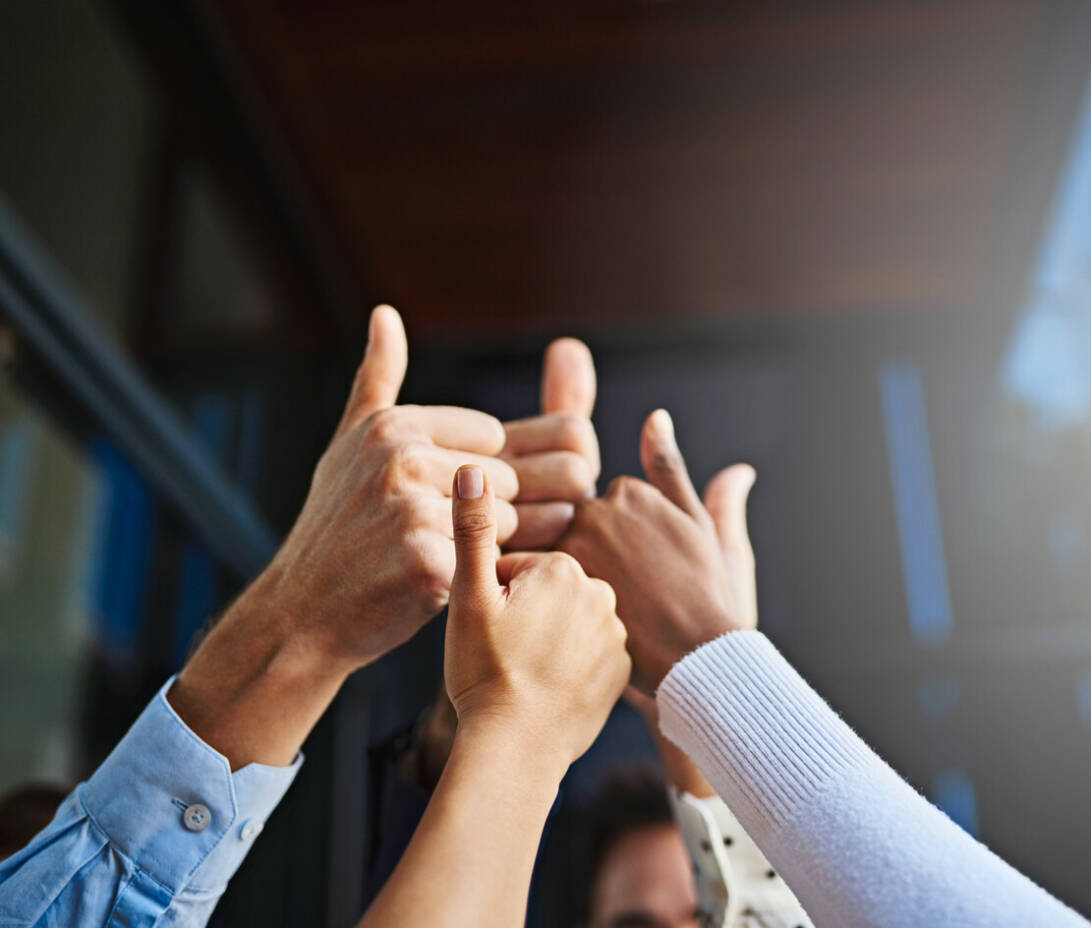
4 months
Project duration
Global
Location
Chemical production
Industry
The ability to monitor risk and react to different scenarios has helped the business achieve an uplift in gross margins of 8%-10%. The organization is now also prepared to mitigate changing legislation, as and when this happens, with recovery options in place and ready to go.
These steps have helped the organization understand not just what actions need to be taken, but when would be the best time to react and mitigate changes in the industry. By considering all the relevant factors, and bringing together all the necessary data, the company can now quickly make complex decisions that will determine the ongoing viability of its plants – ensuring on the ongoing success of the business over the next 10 years.
Results
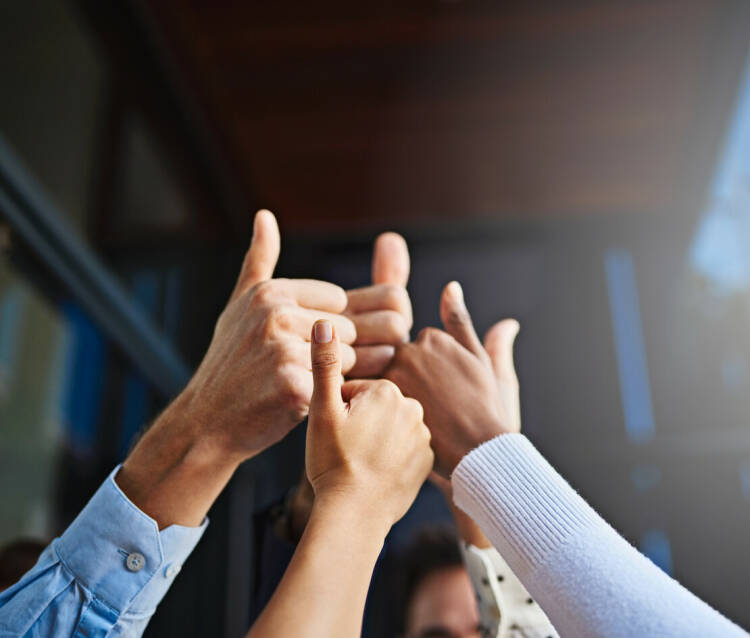
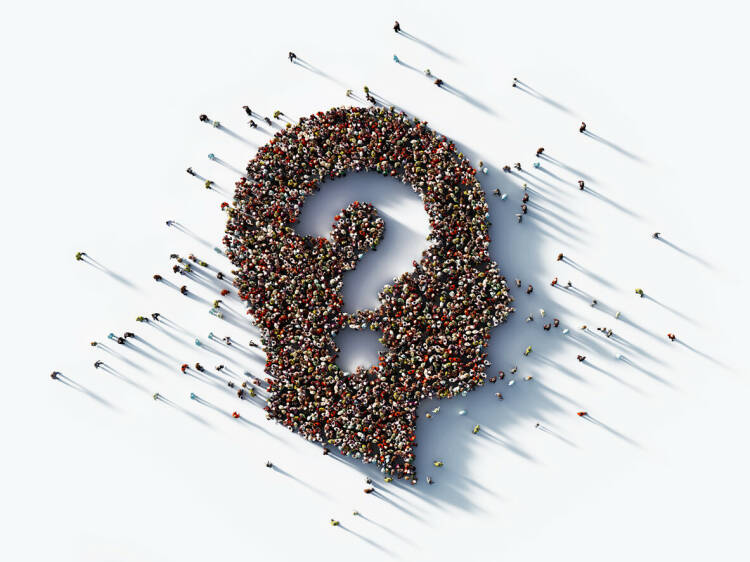
We were able to bring together extensive amounts of information and analyze how each of these risks would impact the business in terms of costs and performance over the long-term.
We demonstrated where the business would likely be in 10 years’ time if no action was taken. We then shared a ‘worst case’ scenario which showed output would decline to just 15% of current volumes. We also highlighted the impact this would have on costs and how it could potentially lead to facilities closing – and how that might lead to the loss of staff and damage the company’s reputation.
We then simulated scenarios that could mitigate the risks. This included exploring substituting raw materials and outsourcing or insourcing certain elements of its operation to save costs. We also developed a reaction plan defined by a series of risk events and mapped out how the business should respond to each risk if they ever came to fruition.
Finally, we created a ‘digital twin’ of the organization which would track operational and financial data. This would enable the business to set an alert level for each risk event.
The solution
The business challenge
4 months
Project duration
Global
Location
Chemical production
Industry
A European multinational chemical company could see that its product line was going to be significantly affected by several changes taking place in the industry.
New regulations in Europe meant key chemical components would no longer be permitted and this was going to have a huge impact on the market. The removal of these raw materials would mean certain products would need to be discontinued, while others would require alternative components to be introduced. These changes were going to affect the organization’s output capacity – and were already affecting its gross margins.
Alongside this, major developments in automation were quickly transforming the industry. Forecasts by the organization showed that if innovation continued at the same pace, demand for specific products from the buying industries would dramatically diminish.
While the business had access to the data needed to monitor key performance metrics across its value chain, it was struggling to interpret the information and understand how it could help to mitigate the risks it faced.
Managing supply chain risk in a rapidly changing chemical industry
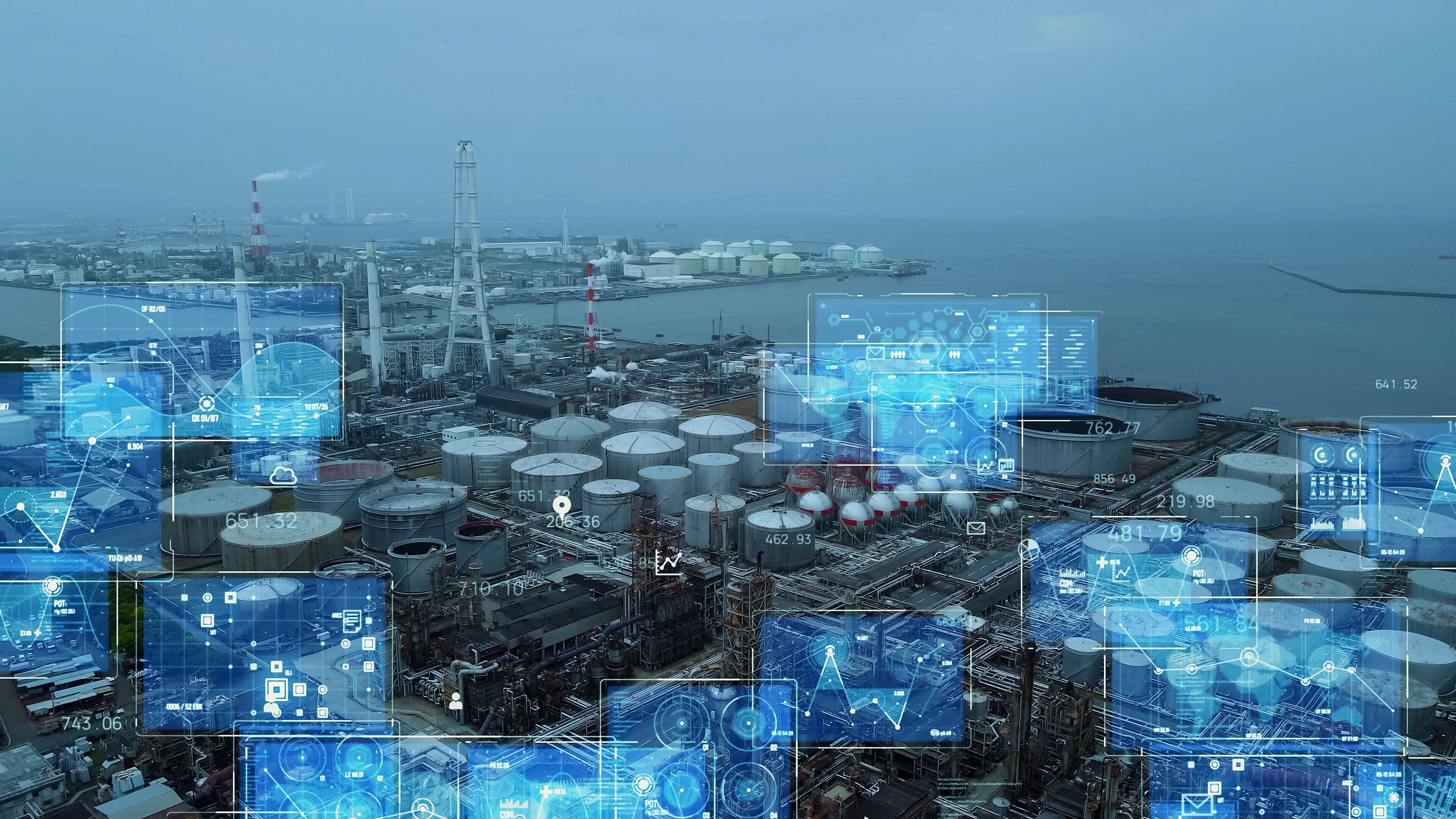