Results
Solution
The business challenge
Increasing workforce capacity by implementing a more collaborative organizational setup
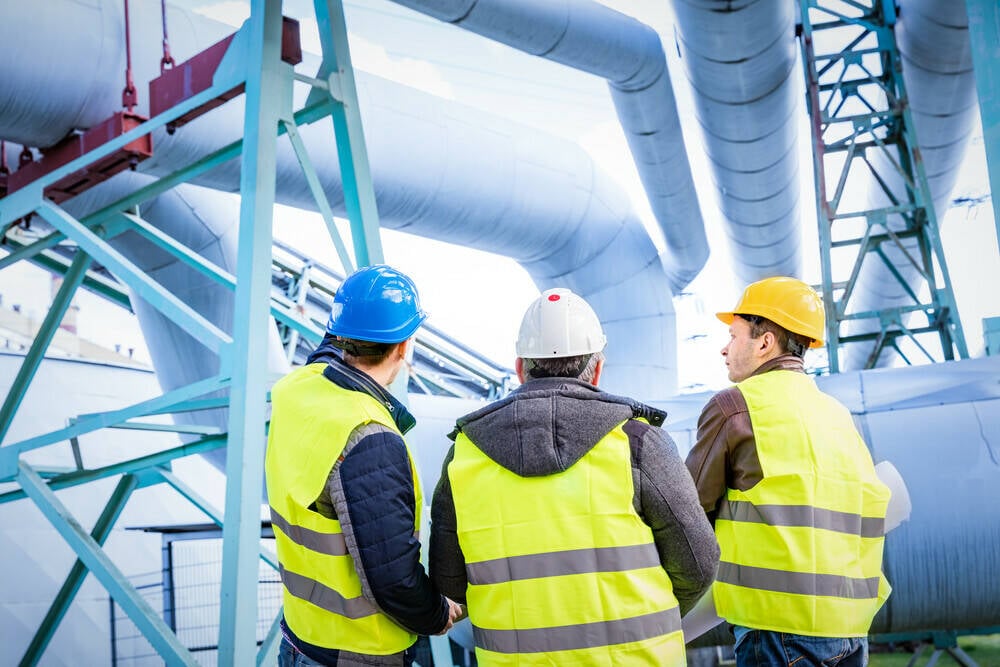
The business challenge
In response to increased competition in its market, a multi-national chemical manufacturer wanted to remove inefficiencies from its CAPEX projects and ensure it was building the best possible solutions for the future.
It recognized that despite possessing vast experience in the design and build of plant equipment and infrastructure, the know-how held within its global engineering team wasn’t being utilized.
A reason for this was a reluctance from business side of the organization to include their engineering colleagues in discussions at the early stage of an investment. Instead, the engineering function was being treated more as a supplier that would be expected to deliver projects, after decisions were already taken.
This had created a scenario where the engineering team, which included several hundred experts, was increasingly being isolated. With limited understanding of the organization’s needs, it was also reluctant to offer the type of advice that could help the business build better, more reliable, and cost-effective solutions.
This problem was further exacerbated by decoupling within the engineering function itself, which had several regional hubs operating autonomously. These independent teams were working from different standards and asset catalogues and, as a result, were developing assets that had a diverse technology base. This limited their ability to build on and learn from each other’s solutions.
There was also limited reflection processes that enabled a structural review of learnings from previous projects. This meant no system was in place to turn those learnings into new standards, which would then be rolled out as new practices in the organization.
The solution
The organization wanted to increase information sharing and collaboration to ensure its solutions were the best they could be, project delivery was more efficient, and the company was enabling continuous improvement.
The first step in this process, was to bring the engineering and business teams closer together in an adapted organizational structure. The intention was to create co-ownership over projects by ensuring all stakeholders understood the business requirements and would be able to provide advice at the most appropriate times.
To ensure ongoing alignment between different business units, a senior engineer and business counterpart were appointed to lead this new setup. Competency centres were also established to share know-how and best practice – and these included international ‘bridgeheads’ that would help prevent regional decoupling.
To enable continuous improvement, skills requirements were identified to drive the ongoing development of existing personnel and inform future recruitment policies. Common standards were also put in place to ensure when best practice was captured and exchanged it was relevant to everyone.
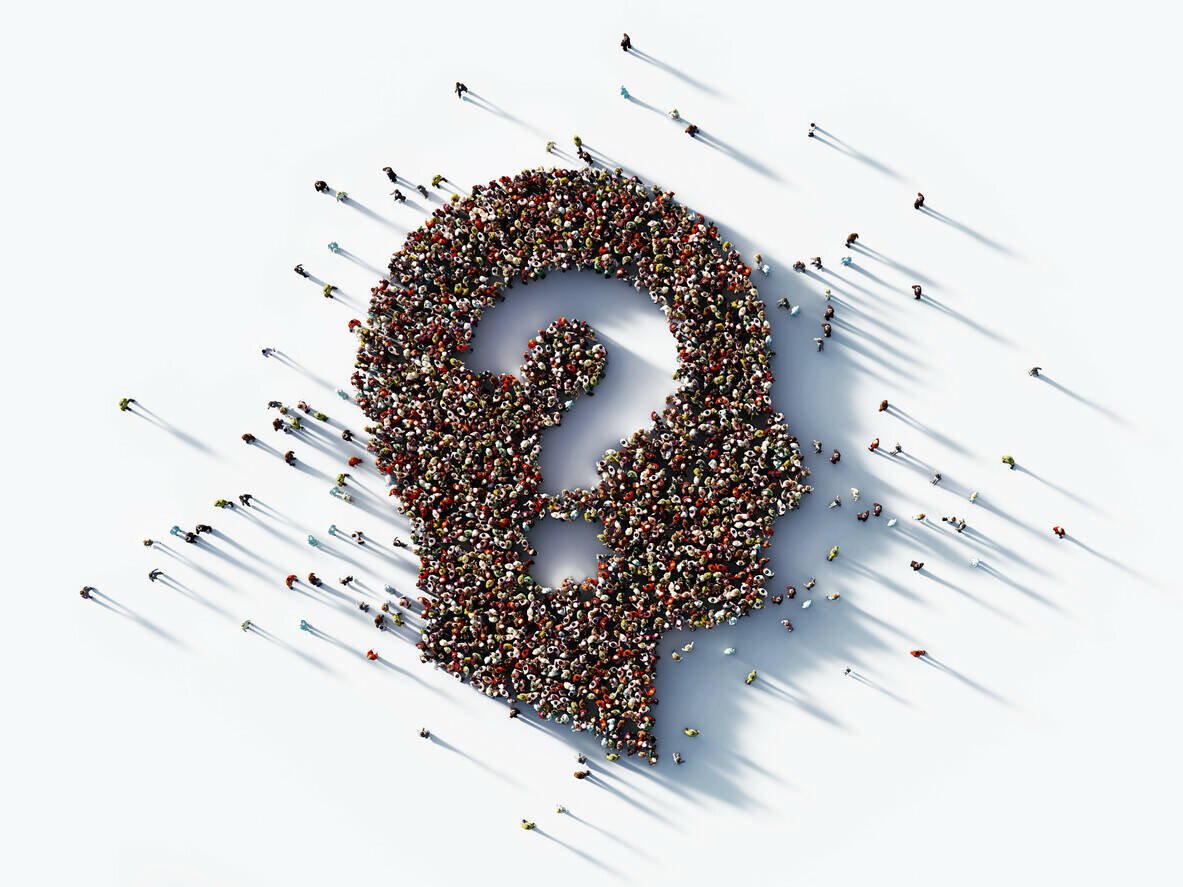
Results
This new setup has harmonized ways of working and helped to drive improvement in both engineering and the quality of interactions taking place.
By improving collaboration and using its collective know-how better, engineering capacity has also increased by more than 10% – diminishing the need to enter the employment market and compete for scarce talent or look for external support.
This has also allowed the organization to commit resources to the deployment of advanced process controls and smart manufacturing.
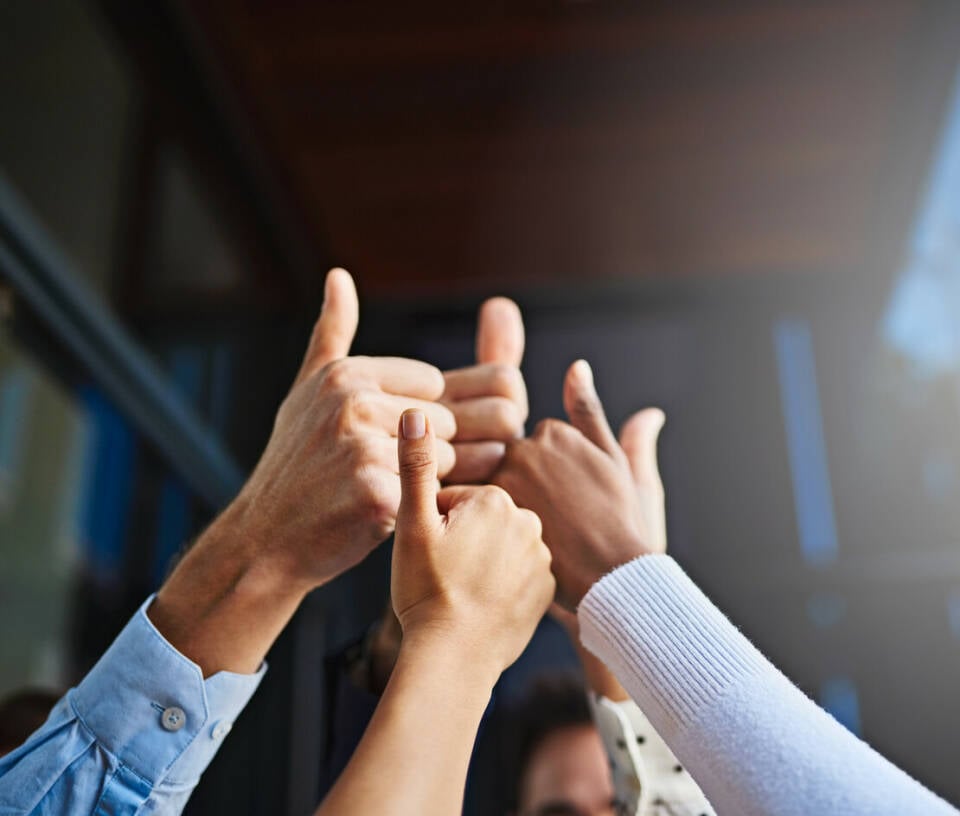
9 months
Project duration
Global
Location
Chemical
Industry
This new setup has harmonized ways of working and helped to drive improvement in both engineering and the quality of interactions taking place.
By improving collaboration and using its collective know-how better, engineering capacity has also increased by more than 10% – diminishing the need to enter the employment market and compete for scarce talent or look for external support.
This has also allowed the organization to commit resources to the deployment of advanced process controls and smart manufacturing.
Results
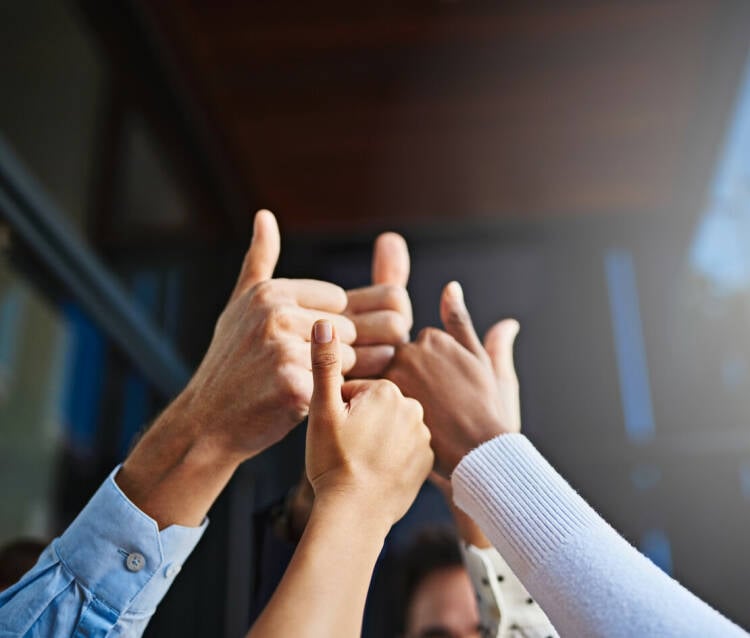
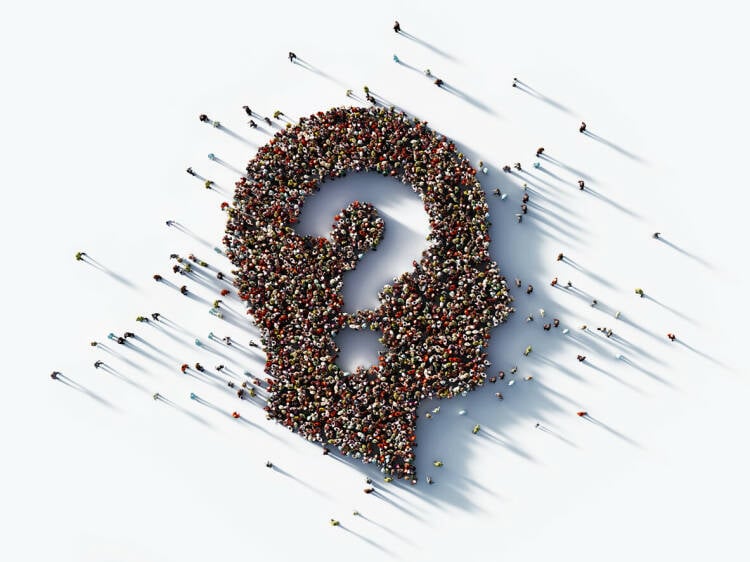
The organization wanted to increase information sharing and collaboration to ensure its solutions were the best they could be, project delivery was more efficient, and the company was enabling continuous improvement.
The first step in this process, was to bring the engineering and business teams closer together in an adapted organizational structure. The intention was to create co-ownership over projects by ensuring all stakeholders understood the business requirements and would be able to provide advice at the most appropriate times.
To ensure ongoing alignment between different business units, a senior engineer and business counterpart were appointed to lead this new setup. Competency centres were also established to share know-how and best practice – and these included international ‘bridgeheads’ that would help prevent regional decoupling.
To enable continuous improvement, skills requirements were identified to drive the ongoing development of existing personnel and inform future recruitment policies. Common standards were also put in place to ensure when best practice was captured and exchanged it was relevant to everyone.
The solution
The business challenge
9 months
Project duration
Global
Location
Chemical
Industry
In response to increased competition in its market, a multi-national chemical manufacturer wanted to remove inefficiencies from its CAPEX projects and ensure it was building the best possible solutions for the future.
It recognized that despite possessing vast experience in the design and build of plant equipment and infrastructure, the know-how held within its global engineering team wasn’t being utilized.
A reason for this was a reluctance from business side of the organization to include their engineering colleagues in discussions at the early stage of an investment. Instead, the engineering function was being treated more as a supplier that would be expected to deliver projects, after decisions were already taken.
This had created a scenario where the engineering team, which included several hundred experts, was increasingly being isolated. With limited understanding of the organization’s needs, it was also reluctant to offer the type of advice that could help the business build better, more reliable, and cost-effective solutions.
This problem was further exacerbated by decoupling within the engineering function itself, which had several regional hubs operating autonomously. These independent teams were working from different standards and asset catalogues and, as a result, were developing assets that had a diverse technology base. This limited their ability to build on and learn from each other’s solutions.
There was also limited reflection processes that enabled a structural review of learnings from previous projects. This meant no system was in place to turn those learnings into new standards, which would then be rolled out as new practices in the organization.
Increasing workforce capacity by implementing a more collaborative organizational setup
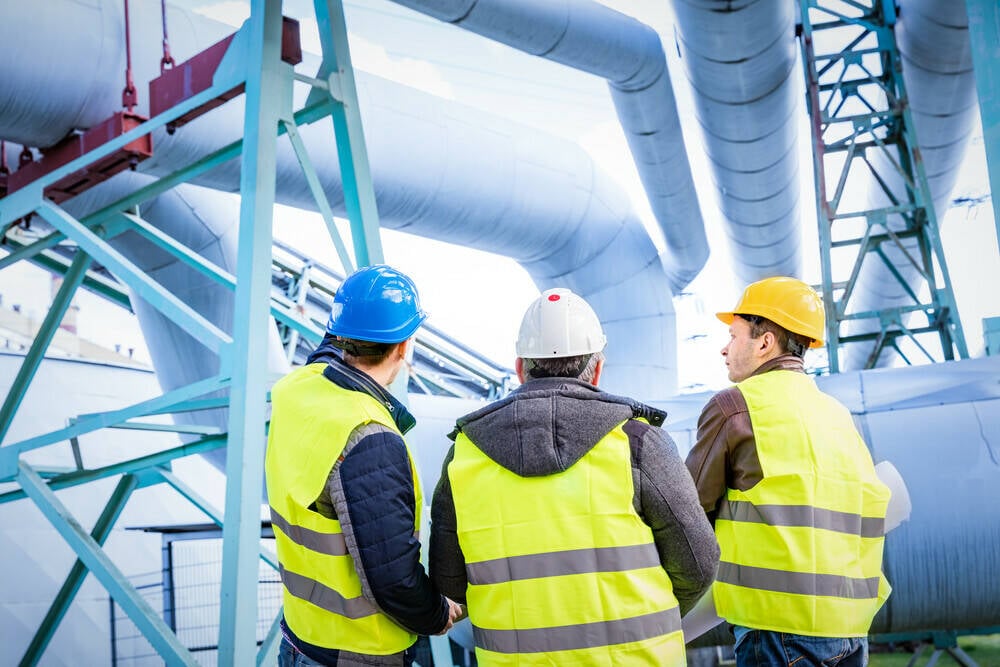